The heat is on!
Operating within a closed environment at temperatures of 1650°C (3000°F) and subject to centrifugal forces generated by a high speed internal vortex, the Vertical Vortex Oxidizer achieves complete thermal treatment of post-diversion residual wastes. The highly turbulent design of the vortex, maximizes heat transfer, converting the RDF / SRF into valuable renewable energy.
The fuels and minerals provided to the VVO thermal treatment unit is MYT are homogenous in nature and permit an optimal extraction of energy. The energy recovery (as electrical net output) averages 30% based on a Higher Heating Value of the MSW of 5500 BTUs/lb. and an average of 20% moisture content (max.).

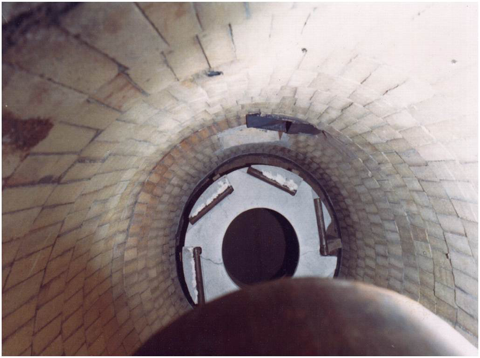
The mineral fragments create a molten glass liner on the surface of the internal ceramic inner wall of the cylindrical combustion chamber. A build-up of this material quickly reaches the shear strength of glass. The inner layer of glass (hottest) overcomes the upward forces of the vortex, begins sliding towards the water base of the combustion chamber, where it is quenched and removed as non-hazardous vitrified slag—representing between 5% to 10% by weight of the input materials.
Particulate from any incomplete combustion, should it occur, impacts the molten wall and is held long enough to effect complete combustion or is rejected into the water base and removed as part of the cooled vitrified slag, from the base of the burner.
It must be understood that the highly turbulent design of the vortex, maximizes heat transfer, conversion of the solid waste to energy, and thus contributes to virtually complete combustion by design.
The retention time within the combustion chamber, virtually a counter flow condition, is upwards of an hour by design. This is unique and unheard of in alternative designs. This in itself assures virtually complete combustion. This molten glass liner protects and extends the life of the combustion chamber’s ceramic liner. All heavier-than-air particles, metal etc., are also subjected to such impingement, retention, and ultimate destruction/conversion to energy.
At these temperatures, the physical characteristics of the combustion unit (ie. -‐vertical vortex configuration) and the contact of the combustion gases with the molten glass wall of this unique energy conversion unit, enables submergence of “heavy metals” salts and various chemical compounds within the SiO2 mélange.
The unique eutectic characteristics of SiO2 in molten and solid stages, does not allow for any crystallization when cooling, and as such at these temperatures, serves as a “blotter” absorbing virtually all the onerous residual contaminants.
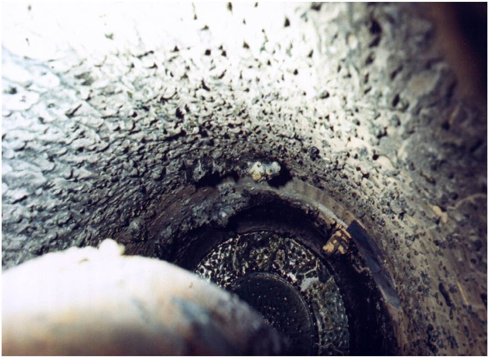
- CARBON MONOXIDE (CO) PRODUCTION — NOT MEASURABLE due to complete combustion,
- NITROGEN OXIDES (NOx) PRODUCTION — NOT MEASURABLE due to complete combustion,
- RESIDUAL METHANE (CH4) — NOT MEASURABLE due to complete combustion,
- PARTICULATE DISCHARGE — NEGLIGIBLE due to complete combustion and impingement,
- TRACE AMOUNTS OF MERCURY (Hg), CADMIUM (Cd), OR COPPER (Cu) (HEAVY METALS) due to the absorbance in the counter flow of molten glass — LESS THAN 10% by weight of input MSW,
- DIOXIN AND FURAN EMMISSIONS — ELIMINATED due to high temperatures of 1650 °C.
This design requires an external energy source to preheat the combustion chamber up to 1100°C. Beyond this threshold, the external energy source is no longer needed and the process becomes self-sustaining with the remaining energy sources being its own «fuel».
The energy recovery (as electrical net output) averages 30% based on a Higher Heating Value of the MSW of 5500 BTUs/lb. and an average of 20% moisture content (max.).